C’est un concept clé de la supply chain. En effet, celle-ci est composée de différents flux, physiques et informationnels. Les flux logistiques comprennent ainsi tous les processus qui échelonnent la vie d’un produit, de sa fabrication à sa commercialisation, en passant par son stockage, son emballage, son transport, sa distribution, etc. Autant dire que chaque flux embarque un certain nombre d’étapes, mais aussi des matières premières ainsi que des ressources humaines et matérielles. Nous vous proposons d’en savoir plus sur les différents types de flux que l’on distingue en matière de logistique ainsi que des solutions pour les gérer et les optimiser.
Les différents flux logistiques
Les flux logistiques sont principalement de deux types :
- Les flux internes, dits aussi flux de production : ils concernent la circulation des matériaux dans le réseau de production et de transformation de l’entreprise. Sont ainsi comprises des opérations comme le stockage des matières premières, l’usinage, la manutention, etc.
- Les flux externes : ils se répartissent en deux catégories.
- Les flux d’approvisionnement : ils se situent en amont de la chaine de production et concernent les mouvements appliqués aux matériaux entre leur fournisseur et l’entrepôt.
- Les flux de distribution : cette fois situés en aval, ces flux concernent les produits finis, voire semi-finis, qui transitent de l’entrepôt vers le client final.
Les stratégies de gestion des flux logistiques
Les méthodes de production impliquent des flux logistiques de différents types, lesquels présentent des avantages et des inconvénients spécifiques.
Les flux poussés ou flux « push »
En flux poussés, la production est fondée sur la prévision de la demande. Cette méthode dite « make-to-stock » consiste donc à produire un bien avant la commande en se basant sur les commandes passées et sur la situation du marché. L’entreprise engage par conséquent des ressources sans être totalement sûre de vendre sa production. Le surstockage et les risques de pénurie en cas de hausse imprévue de la demande sont les principaux inconvénients de cette méthode. Elle ne saurait s’appliquer aux denrées périssables. En revanche, elle participe à renforcer la satisfaction client puisque les délais de livraison sont considérablement réduits.
Les flux tirés ou flux « pull »
Une méthode de production en flux tirés se base sur la demande réelle. La production est lancée quand la commande est effective : elle est « tirée » par la demande. Grâce à ce système, l’entreprise évite la surproduction et le gaspillage. Elle réduit également les frais de stockage. En revanche, les délais de livraison sont rallongés. La méthode « make-to-order » s’applique généralement dans le secteur de l’agroalimentaire. Elle permet par ailleurs à l’entreprise d’être réactive sur des demandes particulières, de personnalisation du produit par exemple.
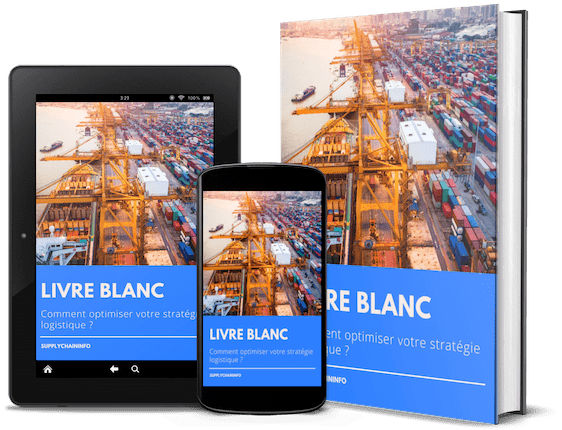
Comment optimiser votre stratégie logistique ?
Les flux tendus ou « just in time »
Quand elle produit à flux tendu, une entreprise mise sur des temps très courts de production et de livraison. Poussée ou tirée, la production est planifiée au plus près de la demande. Le principal avantage de cette méthode tient dans la réduction des stocks et des coûts qui leur sont liés et dans la rapidité des délais de livraison. Elle s’appuie sur une coordination précise de tous les acteurs de la chaine de fabrication puisqu’elle nécessite des approvisionnements réguliers en amont et des fréquences élevées de transport en aval. La production « just-in-time » (JAT) est mise en application dans le secteur industriel, notamment dans le domaine de l’industrie automobile.
Les flux synchrones
Les flux synchrones concernent les flux externes d’approvisionnement. En effet, cette méthode consiste à approvisionner composants, matériaux et matières premières en provenance des fournisseurs au moment de leur utilisation dans la chaine de production. C’est l’industrie automobile qui a initié ce système dans le but d’optimiser la production à flux tendus et de réduire les coûts de stockage des pièces détachées. Là aussi, l’organisation de la chaine logistique est cruciale afin d’éviter les retards de production et de livraison.
Comment optimiser les flux logistiques ?
Les flux étant toujours plus complexes, il est désormais indispensable de déployer des stratégies d’optimisation. Définies en fonction de la méthode de production de l’entreprise et de ses objectifs, elles s’appuient sur :
- La cartographie des flux logistiques afin de mettre en exergue toutes les activités qui la composent, leur nature, leur délai d’exécution, leur enchainement, les ressources qu’elles mobilisent…
- L’identification des processus à améliorer, voire à éliminer, pour gagner en efficacité et en rentabilité
- La définition d’un plan d’actions et d’indicateurs de performance pour mesurer objectivement la portée des actions menées et les ajuster si nécessaire
Comment les intégrer dans sa logistique ?
Pour intégrer et piloter ces mesures d’optimisation des flux physiques, le responsable logistique a à sa disposition différents outils, comme les logiciels de simulation de flux logistiques, les systèmes d’automatisation des flux, les logiciels de gestion de stocks, d’entrepôt, de transport, etc. L’optimisation des flux logistiques s’appuie également sur l’implication des acteurs de la chaine logistique dans cette stratégie et sur la collaboration des différents départements de l’entreprise et de ses fournisseurs. Flux d’informations et flux de marchandises sont ainsi étroitement corrélés.
L’optimisation des flux logistiques au cœur des préoccupations de l’entreprise
La gestion et l’optimisation des flux logistiques permettent à l’entreprise de répondre à plusieurs objectifs : augmentation de la productivité, baisse des coûts de stockage, réduction des temps de livraison… Qui plus est, en limitant le gaspillage et en améliorant la qualité de ses produits et de ses services, non seulement l’entreprise optimise son budget, mais elle renforce également son image de marque et assure sa croissance.
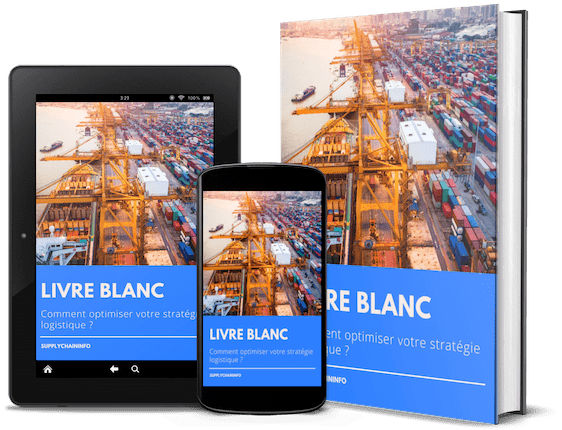