L’entreposition d’une importante quantité de matières premières pour une production ou une importante quantité de produits finis pour la vente est une bonne méthode logistique pour prévenir toute rupture de stock. Toutefois, dans certaines circonstances, cela peut aussi confronter l’entreprise à des risques de sur-stockage. Ce genre de situation peut avoir des répercussions économiques et financières importantes. La gestion des stocks constitue un levier indispensable pour le bon fonctionnement d’un entrepôt, notamment liée au traçage des marchandises : la totalité de la chaîne logistique en dépend. Partant de ce constat, comment faire pour gérer le sur-stockage en logistique de manière optimale ? Découvrons toutes les réponses ici.
Le sur-stockage, qu’est-ce que c’est ?
Le sur-stockage, ou simplement l’excès de stock, est la position dans laquelle peut se retrouver un entrepôt quand les produits finis ou la matière première entreposés à l’intérieur surpassent largement la demande. Dans ces conditions, les entrées de produits sont plus nombreuses que les sorties, ce qui provoque un stock non désiré.
Dans la majorité des cas, cela peut être le résultat d’une mauvaise coordination ou planification de la part du secteur logistique de l’entreprise, ou encore de mauvaises prévisions de ventes ou d’erreurs en production par exemple. Une erreur courante dans de nombreuses entreprises consiste à ne pas attribuer la bonne rotation à un produit et cela peut entraîner un excès de stock. Cela permet d’en déduire que le sur-stockage a la plupart du temps lieu dans le cas d’une installation logistique qui stocke ou approvisionne des produits créés à la chaîne.
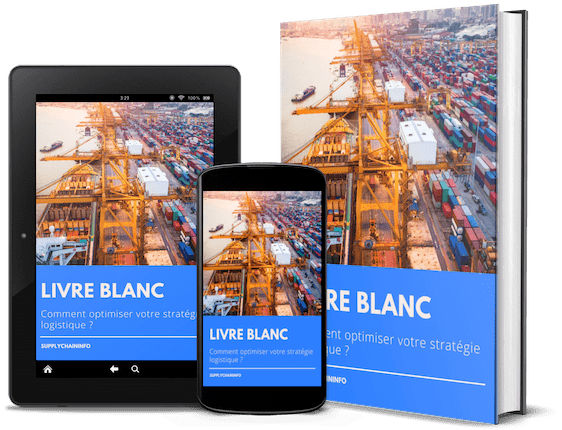
Comment optimiser votre stratégie logistique ?
Comment le sur-stockage est-il généré ?
Un excès de stock peut être la conséquence de nombreux facteurs : la réputation de la marque, la saisonnalité d’un produit, l’arrivée de nouveaux concurrents sur le marché ou encore la dégradation des conditions socio-économiques de ce marché.
Il est facile d’en déduire que les conditions préalables pouvant entraîner un sur-stockage peuvent être dues à :
- des facteurs externes, pouvant résulter de changements socio-économiques extérieurs à l’activité de la société. Dans cette situation, l’entrepôt possède toujours le stock prévu dans son planning logistique, mais la demande du produit a changé. L’entrepôt doit être en mesure de réaffecter les ordres d’entrée et de sortie de ses marchandises s’il souhaite rééquilibrer les choses. Ce cas peut se produire lors d’une crise économique ou d’un changement de mode ;
- des facteurs internes, pouvant résulter d’erreurs provenant de l’organisation directe de l’entreprise. Cela peut concerner des inexactitudes du service achat-vente, qui peut commettre une imprécision dans ses prévisions de ventes ou une erreur logistique (une simple mauvaise gestion des stocks).
Comment faire face à un sur-stockage en logistique ?
Il convient de changer de méthode de stockage, de manière temporaire ou sur le plus long terme. Les professionnels de la logistique ont pris la peine de catégoriser les différentes méthodes de stockage selon le produit concerné (froid, périssable, etc.), tout en prenant en compte la dynamique de vente de ce même produit.
La méthode de stockage ABC
Cette technique pour gérer un stock est très souvent mise en place dans les entrepôts. Le principe consiste à catégoriser les marchandises par ordre d’importance afin de les scinder en catégorie A, B et C :
- une marchandise A possède de la valeur ;
- une marchandise B a une valeur moyenne ;
- une marchandise C dispose de la valeur la plus faible.
Cette pratique permet de mettre en avant les marchandises les plus importantes du stock.
Le stockage des marchandises dans un entrepôt logistique selon cette méthode doit tout de même respecter certaines règles pour être parfaitement efficace, pendant la phase de stockage jusqu’au conditionnement du produit :
- les marchandises A doivent être stockée au milieu des espaces de rayonnage, tout en étant proches des entrées et sorties des marchandises ;
- les marchandises B et C pourront être placées dans les rayonnements alentour, accessibles parfois moins facilement.
Dans ce contexte, il est plus aisé et rapide d’accéder aux produits les plus demandés et ainsi gagner en productivité et d’optimiser le flux des marchandises.
Comment optimiser la manutention des marchandises dans les espaces de stockage ?
Il est nécessaire de garder à l’esprit que pour gérer les espaces disponibles, il est également important de garder un jeu de manutention pour les équipes, en fonction des caractéristiques des marchandises :
- pour des archives : le jeu doit être presque nul afin d’optimiser le stockage logistique ;
- dans le cas d’une manutention manuelle : un jeu haut et latéral (quelques cm) pour saisir la marchandise ;
- si des machines de manutention sont nécessaires : un jeu latéral de 75 mm, ainsi qu’un jeu haut de 10 cm peuvent être mis en place.
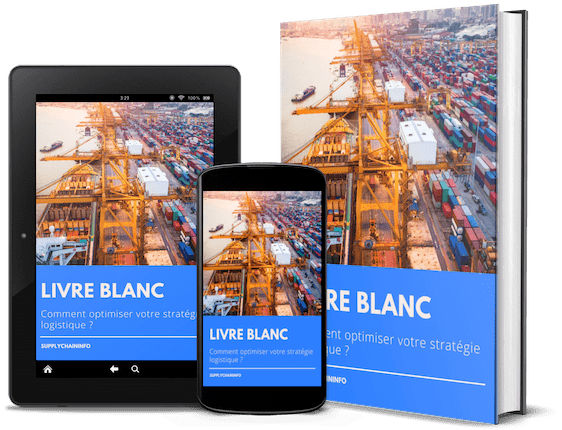
Comment optimiser votre stratégie logistique ?
Utiliser les systèmes LIFO et FIFO pour gérer les flux logistiques
On rencontre deux méthodes qui permettent d’éviter le sur-stockage des produits à l’arrivée et à la sortie du processus.
Le système FIFO
Le système FIFO (first in – first out) est on ne peut plus simple : les marchandises sont chargées d’un côté du système de rayonnage pour être emportées de l’autre.
Cette pratique permet de sortir une marchandise du stock en prenant en compte l’ordre d’arrivée chronologique. Cette méthode est particulièrement recommandée, par exemple pour éviter de perdre des produits périssables. Cette méthode dynamique offre également l’opportunité de mettre en place une manutention en double accès, lors de l’entrée et la sortie des stocks. Cela s’avère très pratique pour que les transporteurs aient facilement accès aux colis prêts à la livraison par exemple.
Le système LIFO
Le système LIFO (last in – first out) est l’inverse de la méthode précédente : la dernière marchandise rentrée devient la première à sortir du stock.
Cette technique fonctionne sur le principe de l’empilement et n’a pas besoin de jeu de manutention en double accès. Si la marchandise stockée ne possède pas de date de péremption ou est sans limites de durée d’utilisation, cela reste la méthode la plus conseillée.
Comment faire pour anticiper un risque de sur-stockage ?
Le sur-stockage peut engendrer des effets très négatifs pour une entreprise. C’est pour cette raison qu’il est bon d’anticiper la bonne gestion des stocks afin de diminuer les risques. Si la cause principale de ce dysfonctionnement est, par exemple, une mauvaise rotation du stock, il serait peut-être nécessaire de mettre en place une meilleure rotation des produits et des marchandises entreposées.
Une autre cause pouvant développer un sur-stockage reste l’organisation du réapprovisionnement qui peut être mauvaise : effectivement, cela peut arriver de commander une marchandise alors qu’il n’en manque pas dans l’entrepôt. Pour empêcher cet excès de stock et les dépenses inutiles que cela engendre, l’entreprise doit chercher son juste équilibre entre régularité d’approvisionnement et rotation des stocks.
Pour mieux gérer et anticiper le sur-stockage en logistique, il est recommandé d’utiliser un système de gestion d’entrepôt (WMS). Ce type d’outil logistique est en mesure de prévoir les besoins précis d’un stock, en fonction des demandes et de leurs caractéristiques. L’entreprise optimise ainsi considérablement son flux de travail, en évitant tout excès de stock des références. De plus, ce logiciel permet de prévoir le meilleur emplacement pour une marchandise, afin d’anticiper l’itinéraire de picking le plus approprié et ainsi favoriser la productivité de toute cette installation.
Nous vous recommandons ces autres pages :
- Quels sont les avantages de la gestion logistique pour une entreprise ?
- Comment améliorer l’organisation logistique d’une entreprise ?
- Comment bénéficier d’un avantage concurrentiel grâce aux processus logistiques ?
- À quoi fait référence le drop-shipping en logistique ?
- Quels sont les avantages de la logistique inversée ?
- Quelles sont les spécificités de la gestion des retours dans la logistique ?
- Comment intégrer le co-packing dans la logistique d’entreprise ?
- Pourquoi utiliser le cross-docking en logistique ?
- Quand et pourquoi choisir d’externaliser sa logistique d’entreprise ?
- Pourquoi automatiser sa logistique d’entreprise ?